November 15, 2021
Electronic eye will improve inspections of aircraft fuselages
In SWISSMODICS, an EU-funded Clean Sky project coordinated by CSEM, engineers will develop an image sensor that can be incorporated into an aircraft’s composite structure in order to detect damage and defects. The device will make aircraft inspections considerably easier, thereby avoiding the need for extended downtime or disassembly.
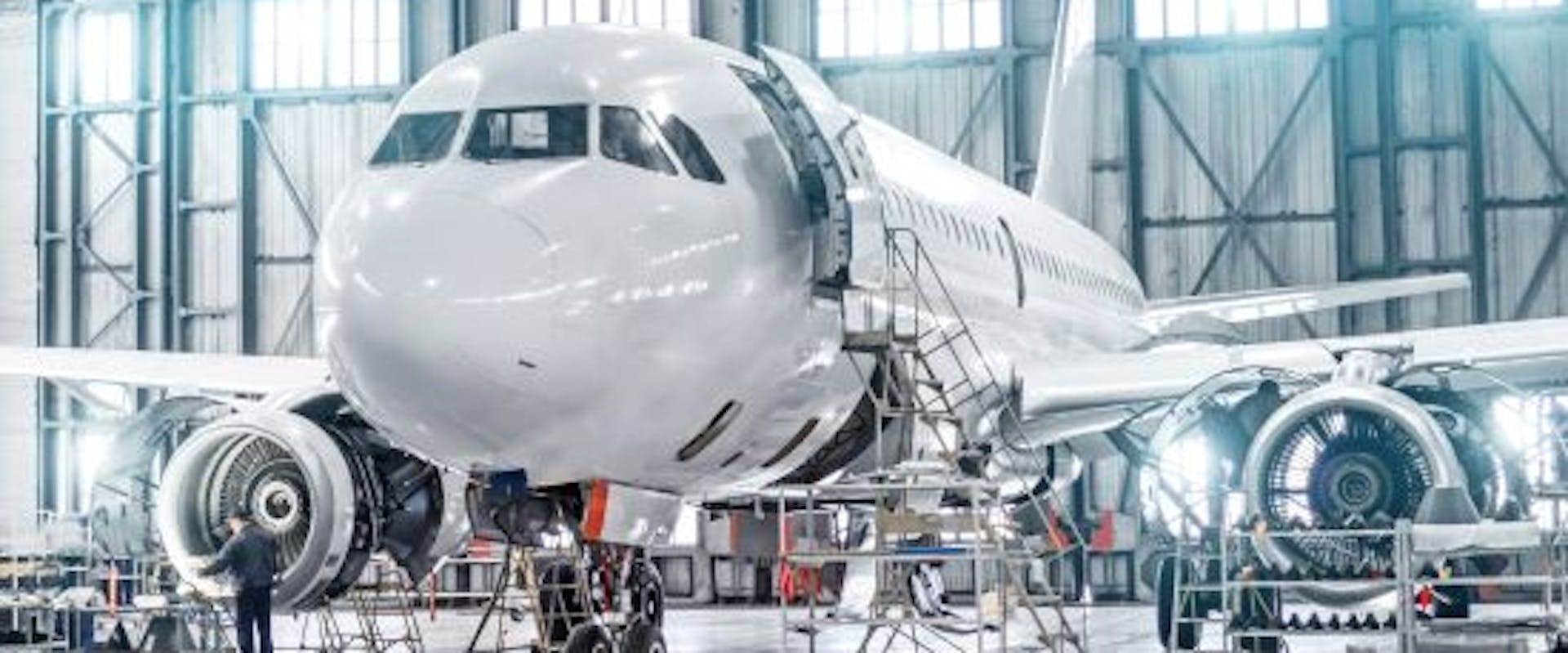